A new version of the MESYS shaft and rolling bearing analysis software including new functionality is available. The bearing analysis software allows the calculation of the load distribution within the bearing as well as bearing life according to ISO 16281. It is integrated in a shaft system calculation offering additional capabilities such as modal analysis, strength calculation for shafts and interfaces to gear calculations. Currently the software is used by customers in 32 countries across 4 continents. The new version is now available under Downloads.
General Extensions
The bearing databases from SKF and NSK are updated. They include standard catalog data. A new bearing database from GMN is added to the installation and includes encrypted internal geometry for spindle bearings including preload values. The databases from CSC and HQW/Barden also containing internal geometry are unchanged to the previous version. Additional encrypted databases containing internal geometry are available from IBC, SPL and GRW, but have to be requested from the manufacturer.
The software is now available in Italian language in addition to English, German, French, Spanish, Turkish, Korean, Japanese and Chinese. Reports can now be generated in a language different from the one set in the user interface.
The parameter variation now includes additional optimization steps for maximizing or minimizing result values and an additional parameter variation only for optimization is available. One example would be the optimization of flank line corrections of gears to achieve an optimal load distribution.
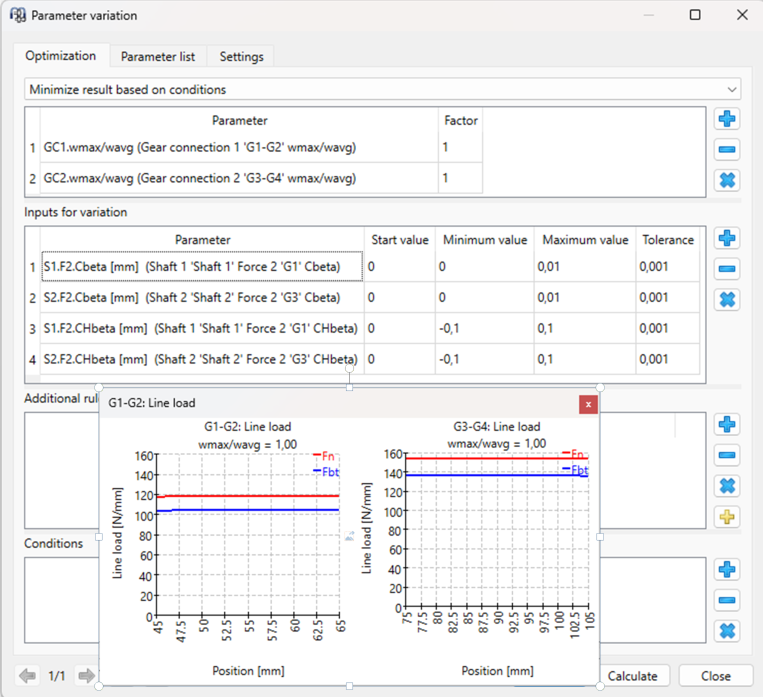
Optimization of flank modifications for optimal line load distribution
Extensions in the Bearing Calculation
The bearing calculation now considers the changes in ISO 16281:2025. The effective roller length Lwe for tapered roller bearings is now defined on the roller cone instead on the axis. The default profile for tapered roller bearings was changed too.
The approximation function for edge stresses now depends on the position of the section instead on the section number. The first image shows ISO/TS 16281 with 41 and 141 sections and the extended pressure calculation, and the second image shows the same according to ISO 16281:
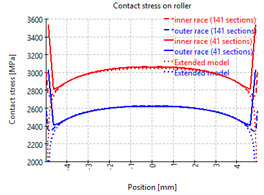
Pressure distribution with edge stress according to ISO/TS 16281
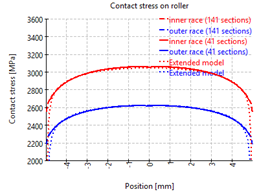
Pressure distribution with edge stress according to ISO 16281
The tolerance tables were updated to the new version ISO 492 (2023-08) of the standard. The updated standard includes a larger diameter range.
Several diagrams for orthogonal shear stress have been added to the software showing the shear stress along various axes. The free tilting angle has been added as an output for deep groove ball bearings.
For ball bearings an additional stress is calculated in case of truncation. This is based on Frantz, P. P. and Leveille “An Approach to Predicting the Threshold of Damage to an Angular Contact Bearing During Truncation”. The stress concentration factor is available as new input.
The contact between the roller end and the shoulder can be evaluated with the updated version. The roller end geometry can be defined using a radius with its centre and the position of the contact ellipse is shown in a diagram.
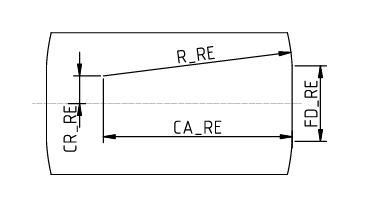
Definition of roller end geometry
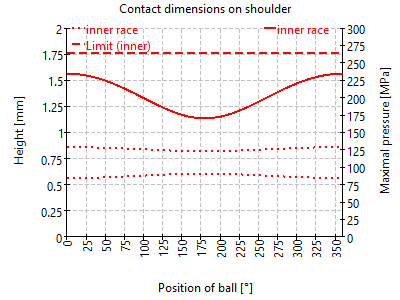
Diagram showing position of contact ellipse and contact stress of roller end contact
Extensions in the Shaft Calculation
For the shaft strength calculation the material strength properties were updated to DIN 743-3:2024, this can lead to smaller changes of safety factors for some materials.
For shaft geometry import as STEP a defeaturing option was added, so that chamfers, fillets or holes can be removed.
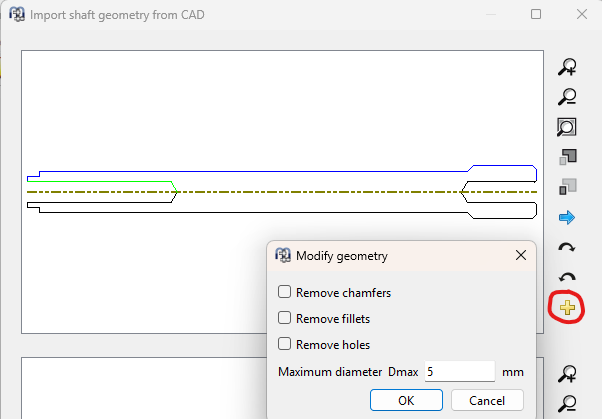
Defeaturing options in shaft geometry import
For 3D-FEA based elastic parts now the nodal results for the surface mesh can be exported as a table.